friction test drilling|what is friction drilling : trade Based on field data and the related theories, the effects of drill string length, rotation speed, trajectory, and drilling fluid density on the friction during horizontal well drilling are analyzed in Sichuan. With increasing the length of . Você vai rir quando eu pedir Pra me fazer mais um favor Dei.
{plog:ftitle_list}
WEBTucano Bet Cassino 2024. Aproveite o Bônus. O Tucano Bet é uma plataforma pioneira para entusiastas de jogos, combinando tecnologia de ponta com uma experiência .
A friction test is a simple procedure involving measurement of pickup weight (PUW), slack off weight (SOW) and free rotating torque (FRT) that provides information about possible changes in. A friction test is a simple procedure involving measurement of pickup weight (PUW), slack off weight (SOW) and free rotating torque (FRT) that provides information about . Friction drilling is one of the most promising methods for hole making in thin sheets of conventional structural alloy materials (aluminum, steel, copper, titanium, etc.) and .
Based on field data and the related theories, the effects of drill string length, rotation speed, trajectory, and drilling fluid density on the friction during horizontal well drilling are analyzed in Sichuan. With increasing the length of .
what is friction drilling
Friction drilling relies on the heat generated from the frictional force between the tool and sheet metal workpiece to soften, penetrate, and deform the work-material into a .Friction drilling is a method of making holes in metal in which the material is pushed out of the way with the aid of heat from friction. The process is also called thermal drilling, flow drilling, . We design and test an algorithm for estimating the bit angular velocity and side forces on a drill string using only topside measurements fed into an adaptive observer. Friction drilling is one of the most promising methods for hole making in thin sheets of conventional structural alloy materials (aluminum, steel, copper, titanium, etc.) and novel polymer.
conduct friction testing of drill pipe specimens 90–203 mm diameter and up to 300 mm long; ensure the drill pipe rotation in both directions up to 150 rpm;mechanical friction will improve drilling efficiency in general, and will in particular enable longer reach for ERD wells. This paper presents results from experimental laboratory tests where . It is worth noting that among the many factors that affect drilling friction resistance, the lubrication performance of drilling fluid is the main adjustable factor. The friction during the drilling process is mixed friction, where part of the contact is boundary friction and the other part is fluid friction. . The four-ball friction tester .
Friction Drilling is a cost-effective, proven, and reliable alternative to traditional fastening methods such as blind rivets, weld nuts, and press nuts. Friction drilling locally displaces material to increase material thickness and create a . Firstly, a equivalent test platform of friction drilling friction characteristics is established based on CA6140 lathe, and the friction characteristics of AISI 321 are studied under the different . A commercial torque-and-drag (T&D) software package is used to show that values for casing friction factor (FF) may be underestimated if sheave friction is present but ignored in the analysis. The results from this study show that an advanced measurement sub placed below the topdrive can provide valuable information regarding drilling performance.
Helicopter Friction Coefficient Test, CAP 437. Cumhuriyet Teknokent Sivas / Türkiye; 0 541 558 00 30; [email protected]; Ulusal Zemin Güvenliği Enstitüsü Helideck . Yavuz Drilling Ship 2022. Anadolu-01 Jack-Up Drilling Platform. Yavuz Drilling Ship Subscribe E-BULLETIN REGISTRATION. Send . National Floor Safety Institute Helideck . Friction is defined as the resistance offered by the surfaces that are in contact when they move past each other. . of friction. Walking, running, writing, sliding, skating, the motion of vehicles, applying brakes to the vehicles, drilling a nail into a wall, etc. are possible due to friction only. Crack RPF Constable and RPF SI 2024 exams .
Friction drilling uses a conical bit made of very heat-resistant material such as cemented carbide.This device is pressed against a target material with both high rotational speed and high pressure. That way, there is a high local production of heat which softens the object, making it plastic.The tool then "sinks" through the object, making a hole in it.UZGEHELİDECK; In a very short time, he specialized in offshore installations and helideck friction testing on ships and received the necessary training. The Helideck Friction Test is performed by a team of trained technicians using the latest friction measurement equipment. Our friction measuring instruments and methodology meet all requirements under UK CAA, CAP .The “friction ratio” is the ratio between sleeve friction and tip resistance, measured as a percentage. Soil type and thereby resistance to liquefaction can be inferred from these measurements. ASTM D-5778 Standard Test Method for Performing Electronic Friction Cone and Piezocone Penetration Testing of Soils.
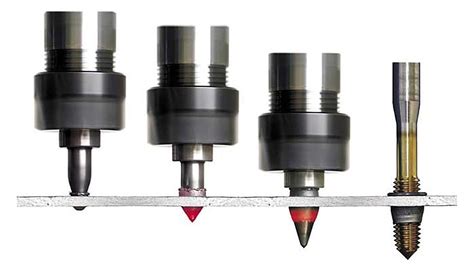
Most of this has, however, focussed on the actual drilling tools (for example see [1], [2] . Friction testing produced generally positive results for the Piotec coating against both sandstone and AISI4140 steel counterfaces, with steel counterfaces producing the lower friction coefficients. Wear testing demonstrated that the Piotec coating .Directional drilling technology plays an important role especially because the horizontal wells have increased oil production more than twofold during recent years. The wellbore friction, torque and drag, between drill string and the wellbore wall is the most critical issue which limits the drilling industry to go beyond a certain measured depth.
drilling bottom hole assembly (BHA) reliability and performance, while reducing the drilling cost and complexity associated with inclined/horizontal well sections. This was to be accomplished by eliminating the need for a downhole drilling tractor or other downhole coiled tubing (CT) friction mitigation techniques when drilling long (>2,000 ft.) friction drilling test was conducted to stop and move back the tool at position A. The workpiece was sectioned and polished to reveal the deformation shape, as shown in Fig. 5 a. The sheet metal workpiece was bent and dented but not perforated. This reveals Fig. 1 Illustration of stages in the friction drilling process
The four-ball friction test revealed that methyl oleate had a coefficient of friction of 0.0018, approximately a third of that for butyl oleate, confirming the simulation’s accuracy. . Everhard, I.; Willis, S.; Villalobos, M.; Clapper, D.; Salem, H.A.; Hughes, B. Reduced Drilling Days and Low Friction Factors Hallmark Eagle Ford Water-Based .
the coefficient of friction, the higher the brine lubricity. As an example, an OFI lubricity tester is utilized to measure the metal-to-metal coefficient of friction when exposed to a variety of brine fluids (Fig. 2). Outcome of the measurement is Coefficient .horizontal drilling. Excessive friction between the drillstring and the casing or the wellbore wall during drilling can greatly limit the rate of penetration (ROP) and create enormous equipment stress (Growcock, 2017). As a result, both solid and liquid lubricants have been used to reduce such friction and improve drilling efficiency.Specialized drilling fluids testing: High-Pressure, High-Temperature Viscometry; Dynamic Fluid-Loss Analysis; Lubricity Coefficient of Friction Measurements for Metal/Metal, Metal/Sandstone, Metal/Shale, Metal/Filter Cake Contact Surfaces; Shale-Fluid Interaction Analysis; A drill-off test is a special drilling test where the drawworks is locked and the string elasticity causes the bit to penetrate the formation at a decreasing weight on bit (WOB).
Drill stem test. A drill stem test (DST) is a procedure for isolating and testing the pressure, permeability and productive capacity of a geological formation during the drilling of a well.The test is an important measurement of pressure behaviour at the drill stem and is a valuable way of obtaining information on the formation fluid and establishing whether a well has found a . As a cost-effective hole production technique, friction drilling is widely used in industrial and automotive manufacturing. Compared with the traditional bolted connection, it enables the fastening of thin metal sheets and thin-walled tubular profiles. Friction drilling results in higher thread length and joint strength, thus better fulfilling the demand for lightweight .drilling process. The base formulation is labeled ‘DQWBM’. Initially samples were prescreened by testing the prospective lubricant in a 3% by volume concentration in one lab-barrel equivalent of fresh water. These samples were hot rolled at 150°F for 16 hours. Coefficients of friction were measured with an R&B lubricity tester (i.e. MM).
friction drilling technology
The Schmitt hammer test is another non-destructive test, where the surface of the concrete is exposed to a compression wave, the reaction force from the surface creates another compressional wave and the amplitude ratio of the two waves can be attributed to the compressive strength of the surface [[5], [6], [7], [8]].This test should be conducted under the .The challenge for mud engineers is to design a drilling fluid system that adequately lubricates the drill string without compromising other physical properties such as density, rheology, and filtration. To test the drilling fluid, engineers use a specially designed Lubricity Tester. This instrument simulates the rotation of the drill string and .Cone Penetration Test (CPT) Interpretation Gregg uses a proprietary CPT interpretation and plotting software. The software takes the CPT data and performs basic interpretation in terms of soil behavior type (SBT) and various geotechnical parametersWhen you are walking, static friction pushes in the direction of you are trying to move (see Figure 2 below). The foot pushes on the ground, and without friction the foot would slide backwards (like walking on ice). Static friction pushes in the direction that prevents your foot from sliding, which results in forward motion.
(11 to 14), obtain the internal friction angle of each rock under the drilling test. The rock internal friction angle obtained from the drilling test was compared with the internal friction angle measured by the laboratory standard test. Second, the internal friction angle obtained from the drilling test is substituted into Eq. 10. By . In order to decrease the torque caused by high frictional forces in drilling, lubricants are used in water-based drilling fluids. To test the performance of lubricants at laboratory conditions, lubricity test is designed to simulate the speed of the rotation of the drill string and the pressure which the drill string bears against the bore hole .
side deltoid tear test
WEBOnline Registration for classes and Courses descriptions. This page aims to help you along your registration process and selection of courses. We advise you to download our .
friction test drilling|what is friction drilling